When it comes to the world of industrial manufacturing, there are countless materials and techniques that play a vital role in shaping the products we use every day. One such technique that often goes unnoticed, yet holds immense significance, is the production of laminated insulation materials. They are the unsung heroes of various industries, providing crucial protection and insulation for a wide range of applications. In this blog post, we will take a closer look at the art of laminated insulation material production and unveil the intricate process behind it.
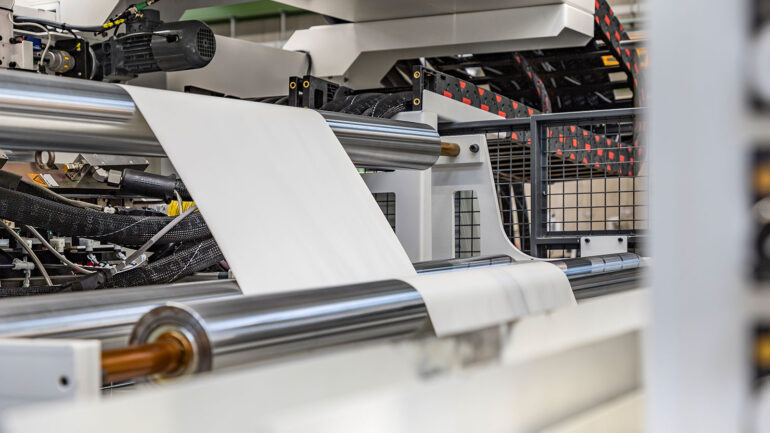
Laminated insulation materials are composite materials composed of multiple layers of insulating ones that are bonded together to create a sturdy and reliable barrier. They find their applications in various industries, including construction, automotive, aerospace, and electrical. They provide thermal insulation, soundproofing, and protection against moisture and other environmental factors. The key to their effectiveness lies in the meticulous production process that ensures each layer contributes to the overall performance of the material.
The journey of laminated insulation material production begins with the selection of the base insulating materials. They can range from fiberglass and mineral wool to foams and films, each offering specific properties suitable for different applications. The chosen ones are then subjected to a rigorous quality check to ensure they meet the desired standards for strength, flexibility, and insulation capabilities.
Once the base materials are approved, the process of lamination begins. They are carefully cut into precise dimensions and arranged in the desired sequence. Adhesive or bonding agents, specially formulated for insulation applications, are applied between the layers to create a strong bond. This step requires great precision to ensure proper alignment and minimal air pockets, as any imperfections can compromise the integrity of the final product.
After the lamination process, the composite material undergoes a curing or drying phase. This step allows the adhesive to fully bond the layers together and harden, resulting in a robust and durable structure. The duration of this phase varies depending on the type of adhesive used and the specific requirements of the material.
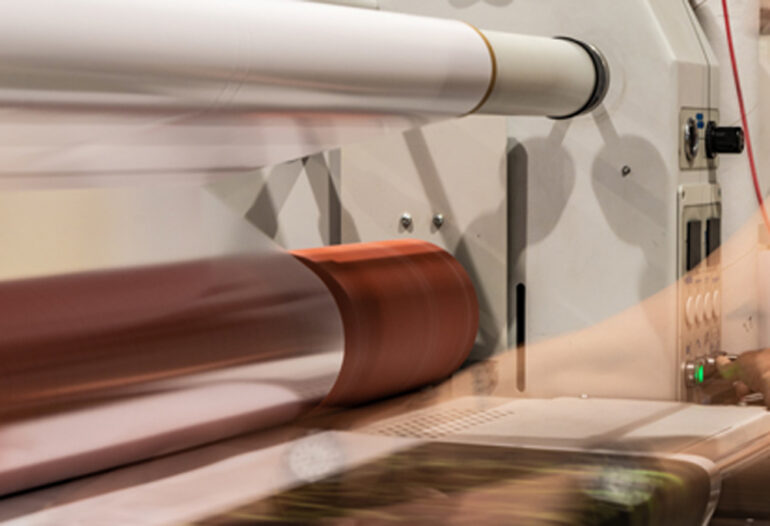
Once it is cured, it goes through further processing to enhance its performance and durability. This may involve additional treatments such as coating, surface finishing, or reinforcement with other materials. These extra steps not only improve the mechanical properties of the laminated insulation material but also provide resistance against chemicals, fire, or other external factors, depending on the intended application.
Quality control is a critical aspect of laminated insulation material production. Each batch of materials undergoes rigorous testing to ensure they meet industry standards and customer specifications. These tests assess factors such as thermal conductivity, tensile strength, fire resistance, and moisture resistance. Only those that pass these stringent tests are deemed suitable for use in various industries.
In conclusion, laminated insulation material production is a fascinating process that combines scientific principles with skilled craftsmanship. So, the next time you step into a temperature-controlled room or drive a quiet car, take a moment to appreciate the artistry behind the laminated insulation materials that make it all possible.